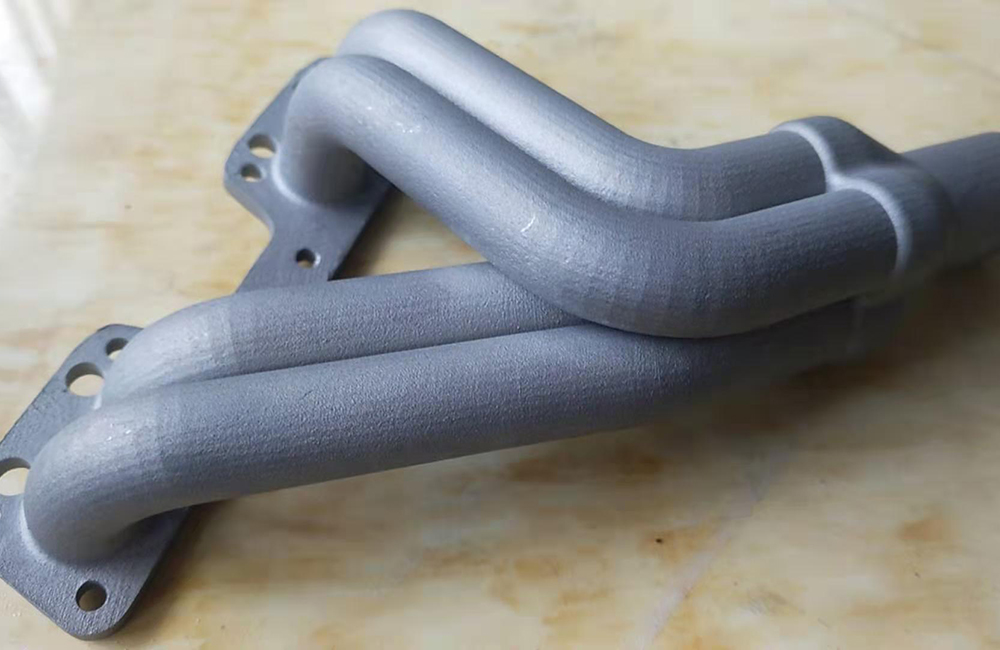
行業/分類:其他手板模型加工
加工方式: 3D打印 使用材料: 金屬
最小精度: 0.1mm 生產周期: 2~7天
產品尺寸: 15cm*10cm*8cm
后處理: 打磨
3D打印金屬管道手板模型具有諸多優勢,以下是詳細介紹:
設計靈活性
復雜結構實現:3D打印技術能夠輕松制造出具有復雜內部結構的金屬管道手板模型。例如,可以在管道內部設計各種形狀的加強筋、散熱通道或流體導向結構,這些結構在傳統加工方式下可能難以實現或需要多道復雜的工序。
個性化定制:根據具體的產品需求和設計理念,快速調整管道的形狀、尺寸、壁厚等參數,滿足不同客戶或項目的個性化要求。比如為特定設備定制特殊彎折角度、異型截面的管道手板模型。
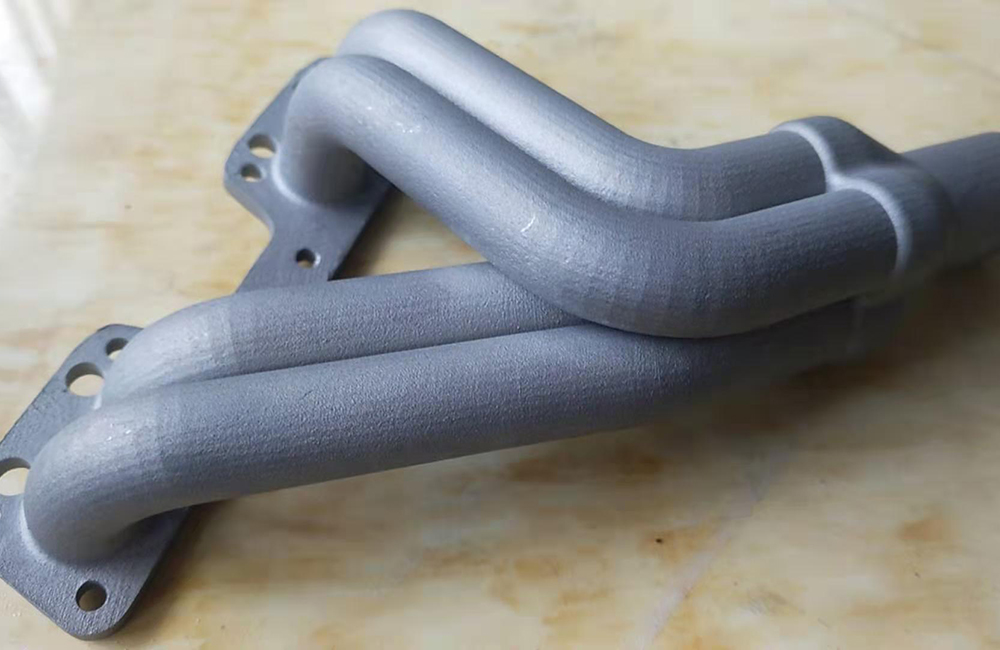
精度與質量
高精度打印:先進的3D打印設備可以實現較高的打印精度,能夠準確地復制設計模型的尺寸和形狀,確保手板模型的尺寸精度符合要求,為后續的產品評估和測試提供可靠依據。
材料性能優良:可選用多種高性能金屬材料進行打印,如不銹鋼、鈦合金、鋁合金等,這些材料具有良好的機械性能、耐腐蝕性和耐高溫性,能夠滿足不同應用場景對手板模型的要求。
縮短研發周期
快速成型:相比傳統的金屬加工方法,3D打印無需復雜的模具制造和長時間的加工過程,能夠直接從數字模型生成實體手板模型,大大縮短了制造周期。例如,一個復雜的金屬管道手板模型,采用3D打印可能只需幾天時間,而傳統加工可能需要數周甚至數月。
同步設計與驗證:在產品設計階段,可以同時進行3D打印手板模型的制作,設計師能夠及時看到實物模型,對設計方案進行直觀的評估和驗證,發現問題后可以迅速修改設計并進行再次打印,加快產品研發進度。
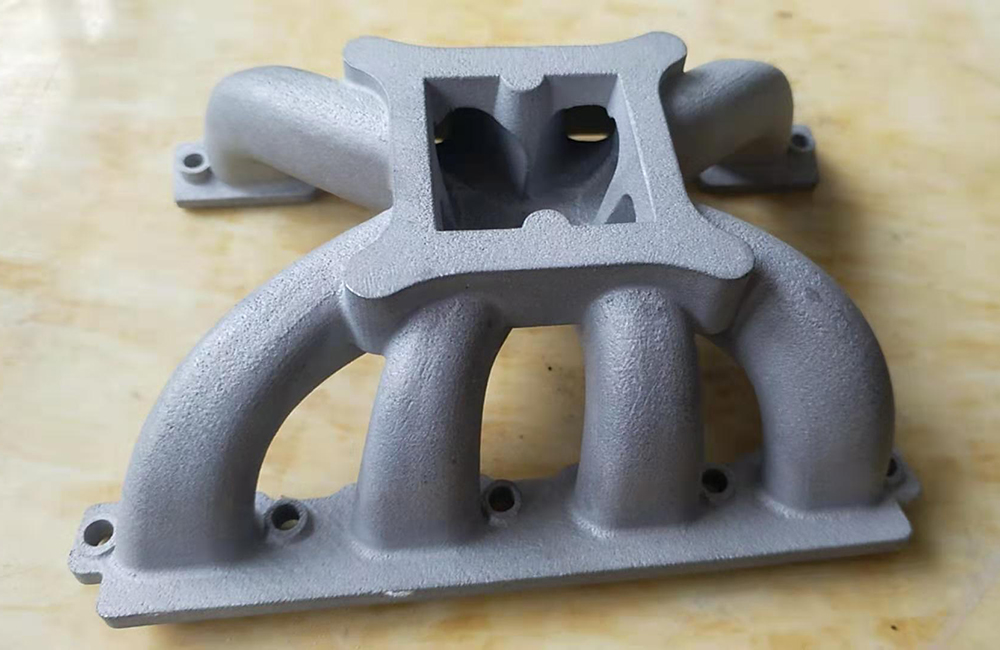
成本效益
降低模具成本:對于小批量或個性化的手板模型制作,3D打印無需制作昂貴的模具,直接節省了大量的模具開發成本,尤其適合在新產品開發初期或多品種小批量生產的情況下使用。
減少材料浪費:3D打印是一種增材制造技術,只會使用與模型體積相當的金屬材料,避免了傳統加工方式中因切割、切削等工藝產生的大量材料浪費,降低了材料成本。
應用案例
航空航天領域:用于制造航空發動機的燃油管道、導氣管路等零部件的手板模型,這些管道通常具有復雜的形狀和嚴格的質量要求,3D打印能夠精確地制造出符合設計要求的手板模型,用于氣動性能測試、裝配驗證等。
汽車制造行業:汽車發動機的冷卻管道、排氣管道等部件的手板模型制作,通過3D打印可以快速驗證管道的設計合理性、與其他零部件的裝配關系以及流體流動特性等,為產品的優化設計提供參考。
工業設備制造:各類化工設備、能源設備中的金屬管道系統,在投入大規模生產前,利用3D打印制作手板模型進行功能測試和流程模擬,提前發現并解決潛在問題,降低生產風險。