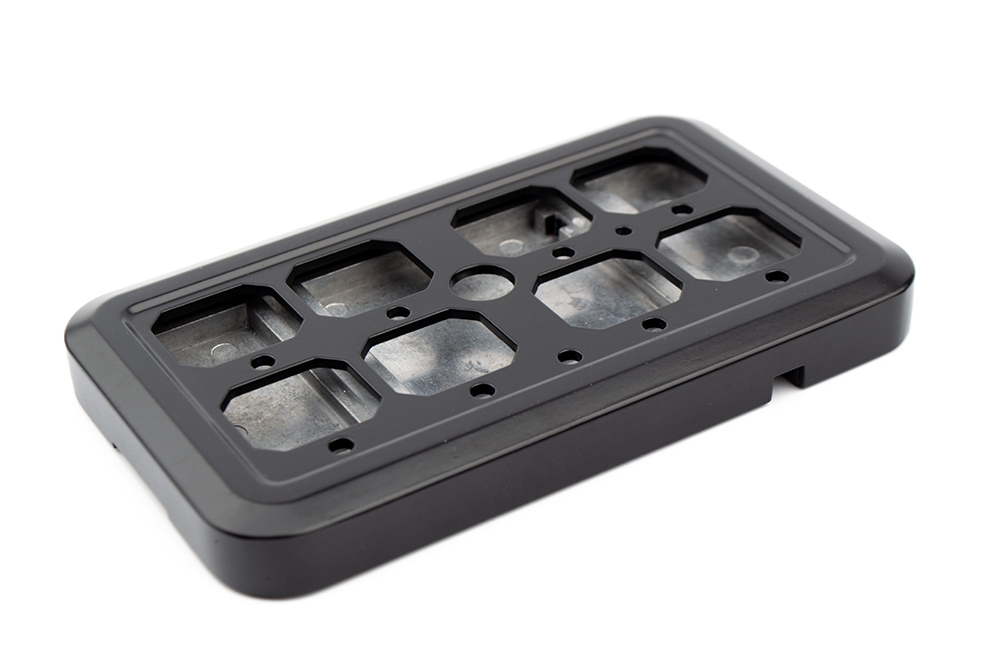
行業/分類:其他手板模型加工
加工方式: 壓鑄加工 使用材料: 鋁合金
最小精度: 0.1mm 生產周期: 2~7天
產品尺寸: 18cm*8cm*2cm
后處理: 打磨
在壓鑄加工電源外殼手板模型時,需重點考慮電磁屏蔽性能、散熱結構、模具設計合理性以及量產可行性。以下是關鍵步驟和注意事項:
1. 材料選擇
- 核心需求:
- 電磁屏蔽:優先選擇鋁合金ADC12(流動性好、成本低)或鎂合金AZ91D(輕量化、屏蔽性能更優)。
- 散熱需求:若需高導熱性,可選純鋁(如AlSi12,導熱系數≈160 W/(m·K))。
- 耐腐蝕性:表面需陽極氧化或電鍍處理(如鍍鎳)。
- 替代方案:
- 小批量驗證可用鋅合金ZA-8(易加工、表面光潔度高)。
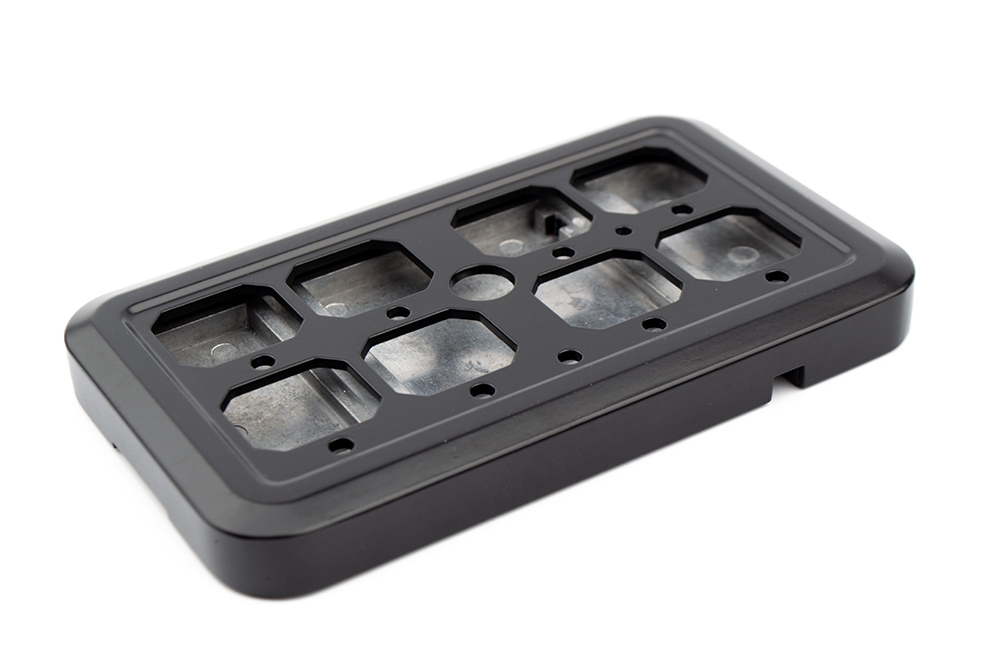
2. 模具設計要點
- 分型面設計:
- 分型線避開外觀面(如Logo區域),隱藏于側面或底部。
- 復雜內腔采用滑塊結構,確保脫模順利(如散熱孔、接口凹槽)。
- 澆注系統優化:
- 澆口位置靠近壁厚區域(如安裝柱),減少填充阻力。
- 流道截面采用梯形設計,降低湍流和卷氣風險。
- 排氣與溢流槽:
- 排氣槽深度0.05~0.1mm,布局在金屬液最后填充區域(如邊角)。
- 溢流槽容量占零件體積5%~10%,用于容納冷料和氣體。
3. 壓鑄工藝參數
- 溫度控制:
- 鋁液溫度:660~680°C(ADC12),模具預熱溫度150~200°C。
- 模溫機分區控溫,確保散熱片區域快速冷卻。
- 壓力與速度:
- 注射壓力:鋁鑄件60~100MPa,薄壁區域(<2mm)需高壓高速填充。
- 壓射速度:3~5m/s,避免金屬液提前凝固。
- 保壓與冷卻:
- 保壓時間≈壁厚×1.5(秒),如3mm壁厚保壓4.5秒,減少縮孔。
- 冷卻時間占總周期30%~50%,通過模溫機精準控制。

4. 結構設計關鍵點
- 壁厚均勻性:
- 主體壁厚2.5~3mm,局部加強筋厚度≥1.5mm(避免應力集中)。
- 散熱片厚度1~1.5mm,間距≥2mm,高度≤15mm(防止填充不足)。
- 安裝與密封結構:
- 螺絲柱根部加圓角(R≥0.5mm),預埋銅螺母(防松動)。
- 接縫處設計0.2~0.3mm密封槽,適配橡膠圈或硅膠墊。
- EMI屏蔽設計:
- 結合導電涂層(如鍍層)或增加金屬接觸彈片結構。
5. 后處理與檢測
- 去毛刺與整形:
- 重點處理分型線、散熱孔邊緣,使用振動拋光或CNC精修。
- 表面處理:
- 噴砂+陽極氧化:提升耐磨性和電磁屏蔽效果(如黑色硬質氧化)。
- 導電噴涂:內壁噴涂導電漆(表面電阻≤0.1Ω/sq)。
- 功能測試:
- 氣密性:施加0.5~1MPa氣壓,檢測泄漏率(≤0.1mL/min)。
- EMI測試:30MHz~1GHz頻段內屏蔽效能≥60dB。
- 散熱模擬:紅外熱像儀監測高功耗區域溫升(對比設計值)。
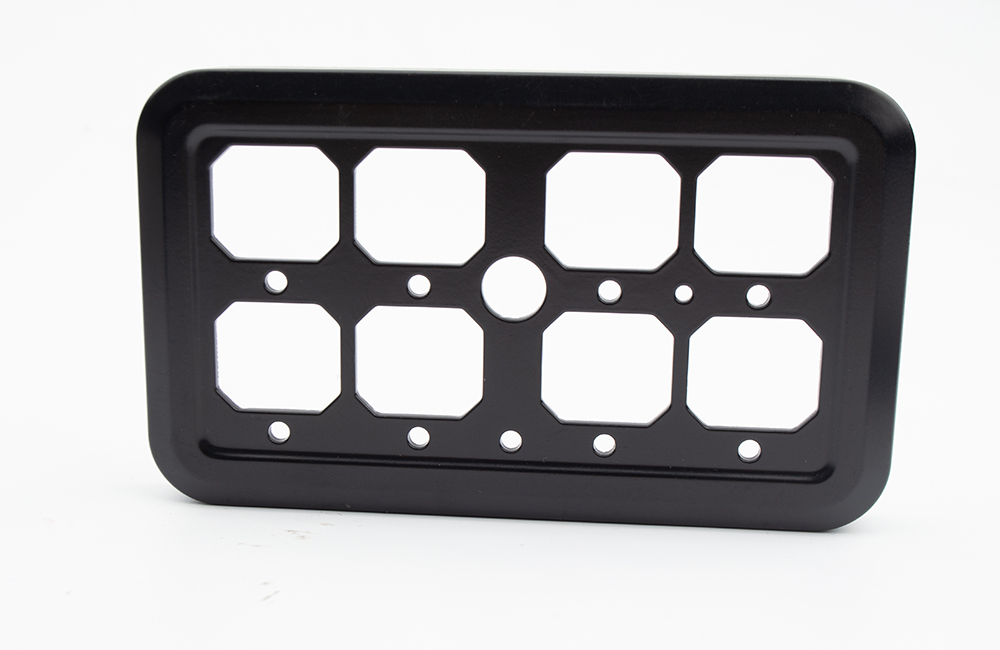
6. 成本控制策略
- 快速試模:
- 使用鋁模(壽命≈5000次)替代鋼模,降低初期成本。
- 3D打印砂芯驗證復雜內腔結構(如散熱風道)。
- 模擬分析:
- 通過MAGMA/ProCAST軟件優化澆注系統,減少試模次數。
- 小批量驗證:
- 首輪試產50~100件,重點檢測尺寸穩定性和裝配兼容性。
7. 常見問題與解決
- 氣孔/縮孔:
- 優化排氣設計,提高注射速度,或采用真空壓鑄。
- 局部加壓:對厚壁區域延長保壓時間。
- 變形翹曲:
- 增加加強筋或調整頂出位置(避免頂針力不均)。
- 時效處理:鋁合金加熱至150°C,保溫2小時釋放應力。
- 表面流痕:
- 提高模溫至200°C以上,減少冷隔。
8. 手板應用場景
- 功能驗證:測試散熱效率、電磁兼容性(EMC)、防水等級(IP67)。
- 客戶確認:提供帶表面處理的全功能樣品,用于訂單確認。
- 小批量交付:替代傳統開模周期,快速響應市場需求(500~1000件)。
9. 替代方案對比
方案 | 優勢 | 劣勢 |
---|---|---|
壓鑄鋁合金手板 | 高精度、量產一致性 | 模具成本高(鋼模≈¥10萬~30萬) |
CNC加工鋁合金 | 免開模、快速迭代 | 成本高(單件≈壓鑄的3~5倍) |
3D打印(SLM鋁) | 適合復雜內腔結構 | 表面粗糙、后處理耗時 |
通過合理設計、精準工藝和嚴格測試,壓鑄電源外殼手板模型可有效驗證量產可行性。若時間緊迫,可結合CNC加工關鍵部位(如精密接口)與壓鑄主體結構,平衡效率與成本。